Fujisash Co., Ltd. is a building materials manufacturer that processes aluminum into products such as curtain walls and window sashes for buildings. In its environmental engineering business operated by a group company, the company supplies plants—including kneaders—that solidify ash generated during waste incineration to municipal incineration facilities across Japan. This business is a groundbreaking application of technology originally developed to solidify aluminum dross generated during aluminum surface treatment, and it holds approximately 50% of the domestic market share. In its logistics business, the company not only manages transportation and warehousing within the group, but also handles logistics for third-party products. Another group company engages in extruded aluminum product sales, manufacturing and selling materials and components for uses beyond construction—such as truck body parts and heat sinks.
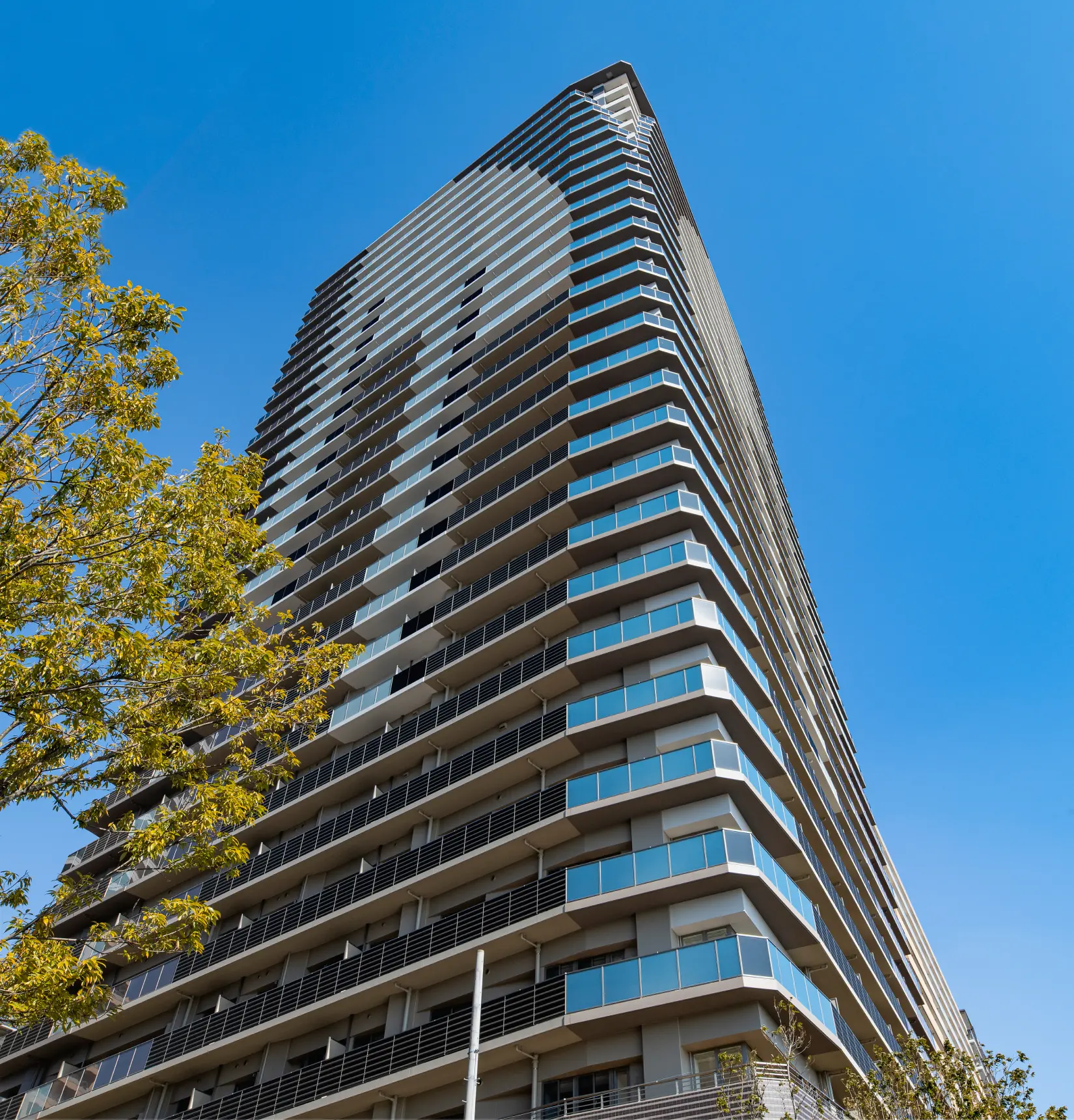
One of Fujisash’s strengths is its integrated production system that spans from sourcing aluminum ingots to processing, installation, and on-site construction. Its primary clients are major general contractors, developers, and housing manufacturers—making it a B2B business model focused on the construction and real estate sectors.
As a manufacturer, the company has been working on energy and CO₂ emissions visualization, both to comply with Japan’s Energy Conservation Act and Global Warming Countermeasures Act, and to support production management. In response to growing societal demands for decarbonization, the company incorporated decarbonized management into its medium-term business plan starting in fiscal year 2022, aiming to strengthen both emissions visibility and disclosure. The shift from voluntary to mandatory TCFD disclosures was one of the catalysts for this initiative. Moreover, requests from business partners prompted the company to pursue SBT certification in 2020, recognizing its role as part of the manufacturing industry’s supply chain.
Upon initiating TCFD disclosure efforts, the company found that it could follow the general guidelines to a certain extent—but struggled to judge whether the collected data and disclosure methods were appropriate. While there was a desire to build internal expertise and minimize reliance on external consultants, the novelty of the undertaking led to the ultimate decision that expert input was essential.
At the time (FY2023), only two employees were responsible for both TCFD disclosure and SBT certification. Given the limited staffing and the need to collect data from suppliers located across the country, the company concluded that it needed consulting support—including assistance with operational workflows for gathering emissions data.
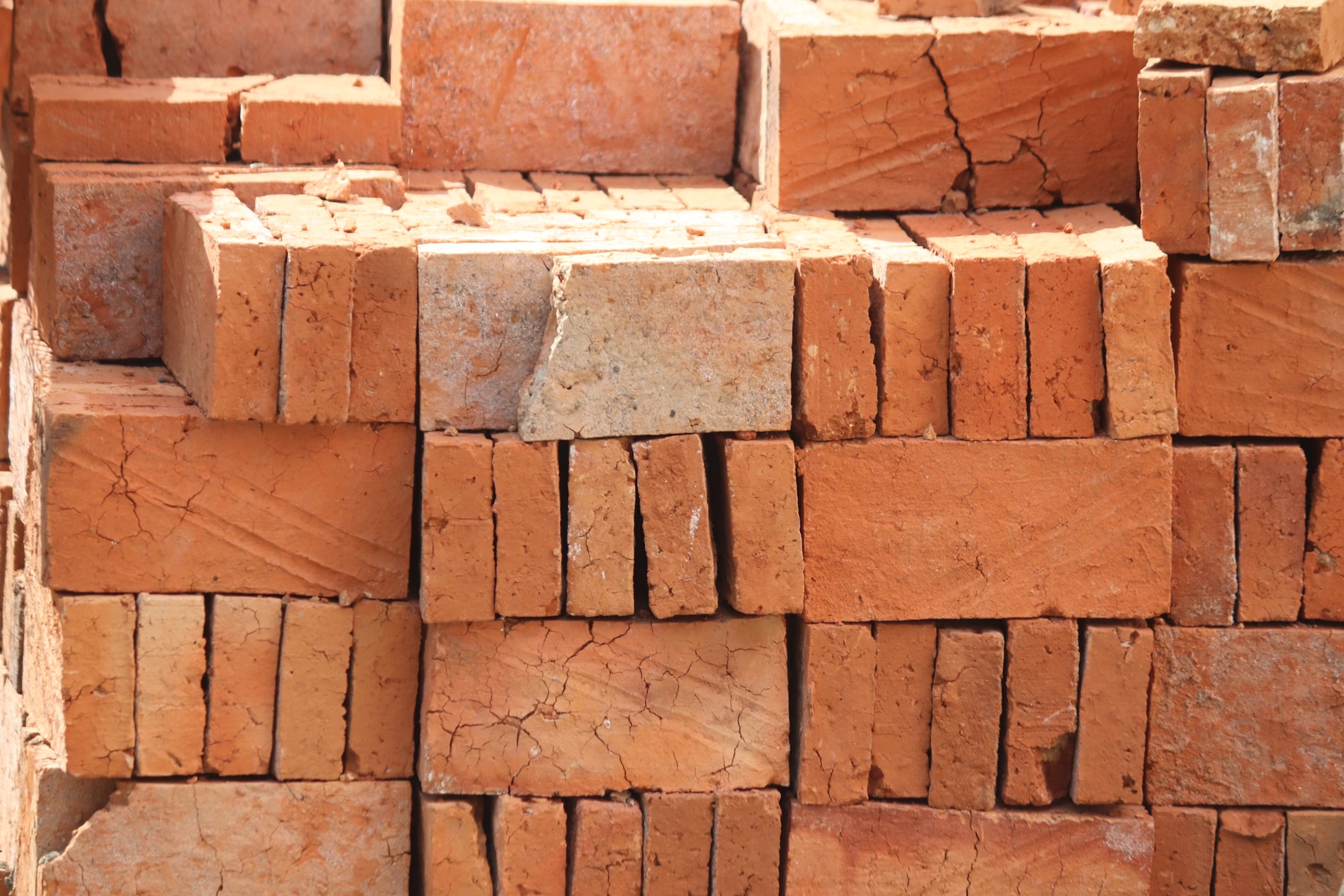
Achieving SBT Certification Just Two Months After Review Began—Thanks to Asuene’s Support
Amid our efforts to gather information on TCFD disclosure and SBT certification, we came across a free seminar hosted by Asuene and decided to attend. After comparing systems from two companies, we concluded that SBT certification—an urgent issue necessary to mitigate business risks—would be best supported by Asuene, given their deeper expertise in this area. One of the key deciding factors was that Asuene had the highest number of implementation achievements at the time.
We first requested TCFD disclosure consulting from Asuene, and their consultants guided us step-by-step through the process. Members from our Administration, R&D, Procurement, Manufacturing, and Sales departments collaborated on the actual work, while Asuene reviewed and validated each stage to help us prepare our disclosures.
Our SBT certification efforts began around 2020, but when it came to calculating Scope 3 emissions, the sheer volume of data and the need for high precision proved to be a major challenge. After successfully working with Asuene on TCFD disclosure, we also decided to seek their support for SBT certification, especially for areas where we lacked full confidence in our calculations. Following our company policy, we handled as much as possible internally, consulting Asuene’s experts whenever uncertainties arose. Roughly 80% of our inquiries were to confirm the accuracy of our own calculations, while the remaining 20% were to ask for clarification or advice on unclear points.
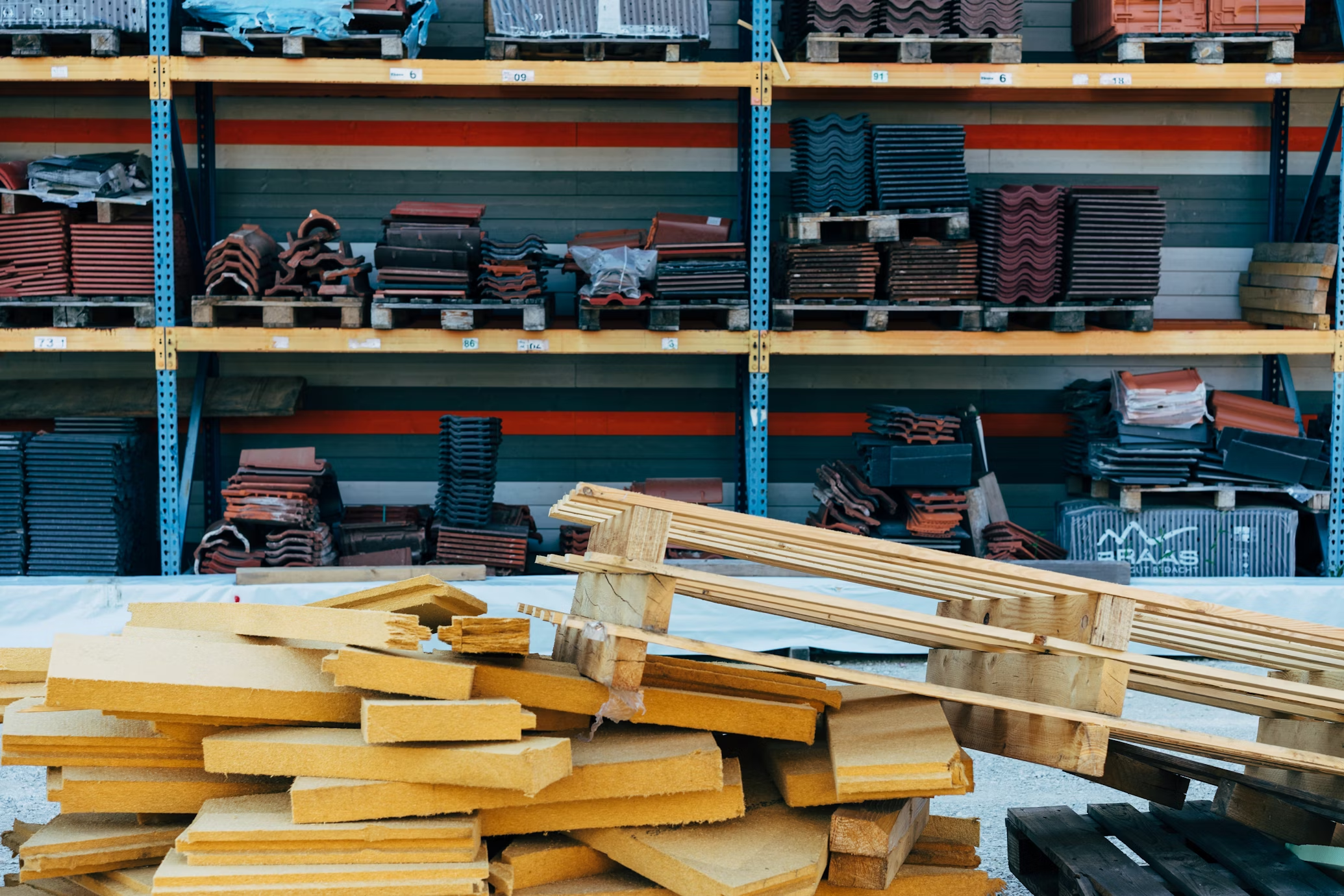
Because SBT certification impacts our entire business, we collected data from departments such as back-office administration and factory operations, with two team members leading the calculation process. Asuene’s consultants were extremely supportive and responsive, and by the time of our first consultation in September 2023, we already felt confident that certification was within reach.
In fact, we submitted our application in December 2023, and the review officially began on April 19. Thanks to Asuene’s guidance, we received our SBT certification on June 13, nearly a month earlier than initially expected—just about two months after the review began.
The SBT Secretariat sent many questions—sometimes more than 20 at once. We were concerned about whether we could respond within the two-business-day deadline. However, Asuene’s consultants always responded swiftly, often delivering proposed answers and precise advice by the next day. We believe it was Asuene’s expert support that enabled us to achieve SBT certification through one of the fastest possible processes—from review start to approval in about two months.
Enhancing Corporate Value by Providing Aluminum Processed Products That Contribute to Green Buildings
We issued a press release announcing the SBT certification we obtained in partnership with Asuene, but beyond that, we have yet to fully leverage it for PR purposes. Moving forward, we plan to actively use the certification in our sales and recruitment efforts. Since SBT certification requires annual progress reporting and renewal at least every five years, we want to keep our internal information up to date and use the achievement as a strategic tool to promote ourselves to clients and create new business opportunities.
Until now, we have visualized our CO₂ emissions as part of our efforts to achieve TCFD disclosure and SBT certification. From here on, however, we are entering the next phase—reducing those emissions. To do so effectively, we believe it’s essential to develop a multi-year investment strategy and roadmap for emission reductions.
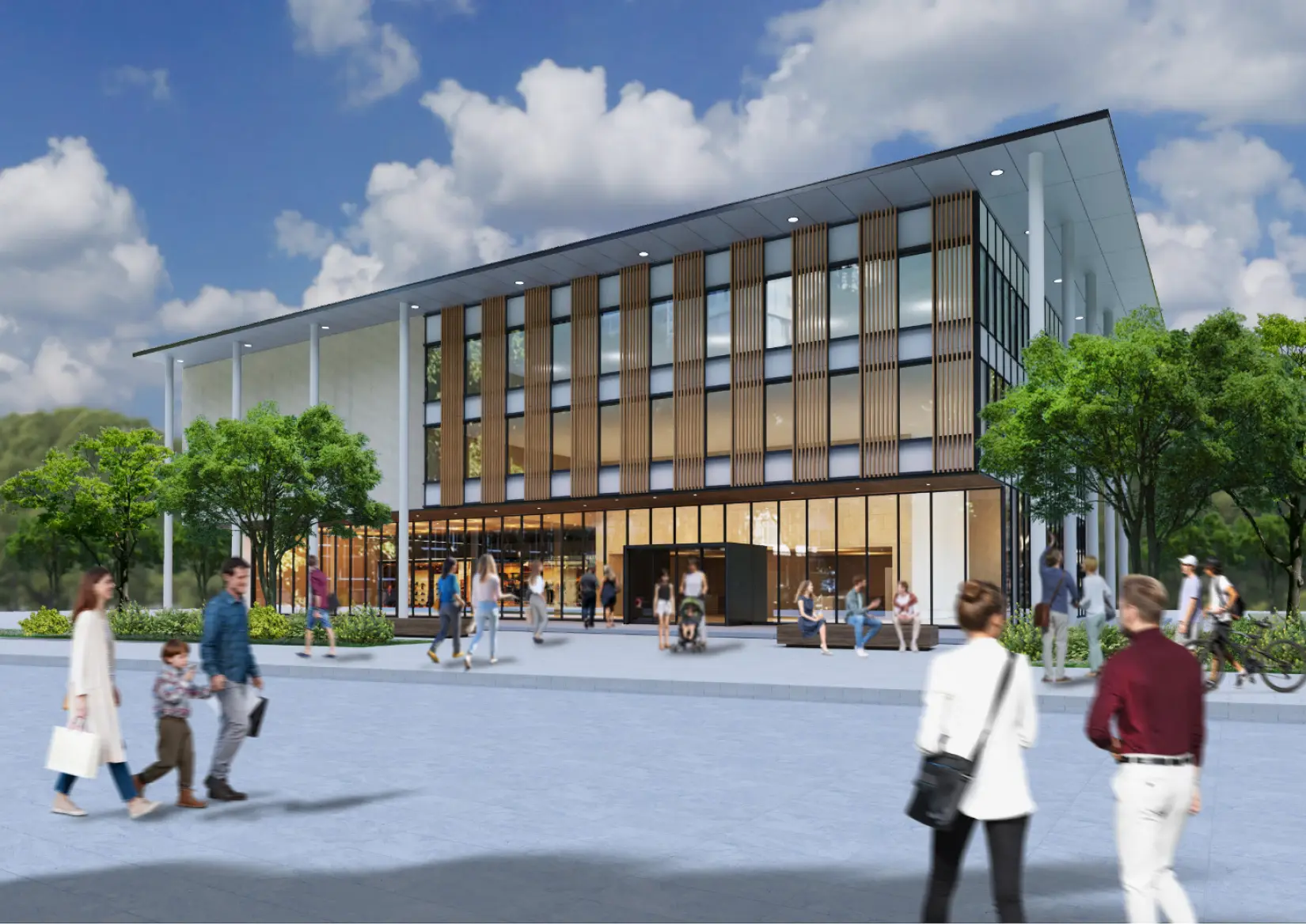
In both the construction industry and academia, initiatives to calculate the carbon footprint (CFP) of buildings are progressing. At the same time, there is growing momentum toward standardizing CO₂ emissions associated with construction activities themselves. It’s possible that in the near future, there will be regulatory caps on CO₂ emissions from new building projects. Anticipating greater demand for low-carbon products and net-zero energy buildings, we are also beginning to work on carbon footprint (CFP) and life cycle assessment (LCA) initiatives. By developing and delivering high-value-added products that contribute to green buildings, we aim to help solve social issues while simultaneously enhancing our corporate value.
As a company that contributes to urban development through building materials, we believe we have a responsibility to protect and enrich people’s lives—both from a business and citizen perspective. Our clients range from major general contractors to small and medium-sized enterprises. Because of this diverse network, we believe we are uniquely positioned to serve as a bridge among companies, sharing a decarbonization mindset and helping to elevate the entire industry.
By taking the lead in promoting decarbonization across the real estate and construction sectors, we hope to contribute to building a society where creating livable, sustainable communities becomes the norm.